Hexamethyl Disiloxane
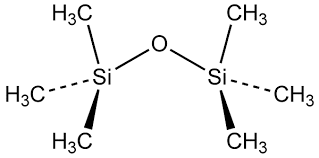
Hexamethyl disiloxane (HMDS), also known as 1,1,1,3,3,3-hexamethyldisiloxane, is a colorless, volatile liquid with a faint, ethereal odor. It is a member of the siloxane family of compounds, which are characterized by the presence of silicon-oxygen-silicon (Si-O-Si) linkages in their molecular structure. HMDS is widely used in the semiconductor industry, as well as in various other applications, due to its unique chemical and physical properties.
History
The history of HMDSO can be traced back to the early development of organosilicon chemistry in the late 19th and early 20th centuries. Siloxanes, the class of compounds to which HMDSO belongs, were first synthesized in the 1930s and have since become an integral part of the silicon-based polymer industry.[1, 2]
Structure of Hexamethul Disiloxane
Hexamethyl Disiloxane (HMDS) is an organosilicon compound with the chemical formula (CH3)3Si-O-Si(CH3)3. It is a colorless, volatile liquid at room temperature and atmospheric pressure.[3]
The structure of HMDS can be described as follows:
- Central Oxygen Atom:
The molecule contains a central oxygen atom, which is bonded to two silicon atoms.
- Silicon Atoms:
The two silicon atoms are each bonded to three methyl (CH3) groups, forming a tetrahedral arrangement around the silicon atoms.
- Methyl Groups:
The six methyl groups are arranged in a symmetrical pattern, with three methyl groups attached to each silicon atom.
CH3
|
CH3-Si-O-Si-CH3
| |
CH3 CH3[4]
Hexamethyl Disiloxane (HMDS) is an organosilicon compound with the chemical formula (CH3)3Si-O-Si(CH3)3. The structure of this molecule can be examined in detail to understand the factors that influence the unique geometry observed.
At the core of the HMDS molecule lies a central oxygen atom, which is bonded to two silicon atoms. Each silicon atom is, in turn, bonded to three methyl (CH3) groups, forming a tetrahedral arrangement around the silicon centers. This tetrahedral geometry is a common structural feature observed in many silicon-containing compounds, as it allows the silicon atoms to adopt a stable configuration by maximizing the distance between the substituents.
However, the Si-O-Si bond angle in HMDS is typically found to be around 145-150 degrees, which is significantly larger than the ideal tetrahedral angle of 109.5 degrees. This deviation from the ideal angle is primarily attributed to the steric repulsion between the bulky methyl groups attached to the silicon atoms.
The presence of the three large methyl groups on each silicon atom creates a substantial amount of steric crowding within the molecule. The methyl groups, being relatively bulky and occupying a significant amount of space, experience significant repulsive forces as they are brought into close proximity. To minimize this steric strain, the molecule adopts a geometry that allows the methyl groups to move farther apart from each other, effectively expanding the Si-O-Si bond angle.
This expansion of the bond angle is a well-known phenomenon observed in organosilicon compounds with bulky substituents. The larger the substituents, the greater the steric repulsion, and the more significant the deviation from the ideal tetrahedral angle. In the case of HMDS, the combination of the three methyl groups on each silicon atom creates a substantial steric hindrance, resulting in the observed expansion of the Si-O-Si bond angle to around 145-150 degrees.
In addition to the steric factors, the electronegativity difference between silicon and oxygen also contributes to the widening of the Si-O-Si bond angle. The partial positive charge on the silicon atoms and the partial negative charge on the oxygen atom create an electrostatic repulsion, further increasing the bond angle to accommodate this electronic effect.
The unique structure of HMDS, with its expanded Si-O-Si bond angle, is a result of the interplay between the steric repulsion of the bulky methyl groups and the electronic factors within the molecule. This structural arrangement allows the molecule to adopt a more stable and energetically favorable configuration, which is crucial for its various applications in the semiconductor industry, organic synthesis, and personal care products.[5]
Mechanism
- Nucleophilic attack:
The hydroxide ion (OH-) from sodium hydroxide (NaOH) undergoes a nucleophilic attack on the silicon atom of chlorotrimethylsilane ((CH3)3SiCl).This is facilitated by the partial positive charge on the silicon atom due to the high electronegativity of the chlorine atom.[6]
- Elimination of water:
The hydroxyl group (OH-) attached to the silicon atom then undergoes an elimination reaction, forming water and a silicon-oxygen-silicon (Si-O-Si) bond. This step is driven by the stability of the Si-O-Si linkage, which is a relatively strong bond.[7]
- Removal of hydrochloric acid:
The hydrochloric acid (HCl) produced in the previous step is then neutralized by the sodium hydroxide (NaOH) present in the reaction mixture, forming sodium chloride (NaCl) and water.[8]
The overall reaction can be summarized as:
2(CH3)3SiCl + 2NaOH → (CH3)3Si-O-Si(CH3)3 + 2NaCl + H2O
The resulting HMDS product has a central oxygen atom bonded to two silicon atoms, with each silicon atom further bonded to three methyl groups. The Si-O-Si bond angle in HMDS is typically expanded to around 145-150 degrees, which is larger than the ideal tetrahedral angle of 109.5 degrees. This deviation is due to the steric repulsion between the bulky methyl groups attached to the silicon atoms.
The versatility of HMDS in various applications is attributed to its unique chemical properties, such as high thermal stability, low surface tension, and ability to act as a silylating agent in organic reactions
Applications
HMDS is widely used in various applications, including:
- Semiconductor industry:
HMDS plays a crucial role in the fabrication of silicon-based semiconductor devices. It is particularly valued as a surface treatment for silicon wafers, where it helps to promote the adhesion of photoresist materials[9]. Photoresists are light-sensitive polymers that are used to create intricate patterns on the wafer surface during the manufacturing of integrated circuits and other electronic components. The ability of HMDS to enhance the wettability and compatibility of the silicon surface with these photoresists is essential for ensuring the precise patterning required in semiconductor device production [10]. By facilitating the effective deposition and adhesion of the photoresist materials, HMDS contributes to the successful fabrication of high-performance, miniaturized electronic devices.
- Organic synthesis:
Beyond its applications in the semiconductor industry, HMDS finds widespread use as a silylating agent in organic chemistry [11].Silylation is a well-established technique that involves the introduction of a silyl group, such as the trimethylsilyl group present in HMDS, onto various functional groups within organic molecules. This process can be employed to protect and activate these functional groups, enabling a wide range of synthetic transformations. HMDS, with its ability to form stable silyl ethers and esters, has become an invaluable tool in the hands of organic chemists, facilitating the synthesis of complex organic compounds, including pharmaceuticals, natural products, and other important molecules.[12]
- Cosmetics and personal care products:
HMDS has also found applications in the cosmetics and personal care products industry[13]. Its unique properties, such as low surface tension and high thermal stability, make it an attractive ingredient in various formulations. HMDS can be incorporated into hair care products, skin care products, and even antiperspirants, where it can provide beneficial effects. For example, in hair care products, HMDS can enhance the spreadability and lubrication of the formulation, leading to improved manageability and styling. In skin care products, HMDS can contribute to enhanced water repellency and reduced greasiness, improving the overall user experience.[14]
- Lubricants and sealants:
HMDS can be used as a lubricant or sealant in specialized applications due to its low surface tension and high thermal stability.[15] The combination of HMDS’s low surface tension and high thermal stability makes it a suitable candidate for use in high-performance lubricants or specialized sealant formulations. In these applications, the unique chemical properties of HMDS can contribute to improved lubrication, reduced wear and tear, and enhanced sealant performance, making it a valuable component in specialized industrial and technological applications.
The wide-ranging applications of HMDS highlight its versatility and importance as an organosilicon compound in modern science and technology. From its crucial role in semiconductor fabrication to its utility in organic synthesis and its inclusion in cosmetic and personal care products, HMDS continues to demonstrate its adaptability and significance across various industries.
Safety and Toxins
- Safety Precautions:
HMDS is a flammable liquid, with a flash point of approximately 12°C (54°F). [16] This low flash point indicates that the substance can readily ignite and pose a fire hazard, particularly when exposed to sources of ignition such as heat, sparks, or open flames. Proper storage and handling procedures are crucial to mitigate the risk of fire and explosion. These include storing HMDS in a cool, well-ventilated area, away from incompatible materials, and using appropriate personal protective equipment (PPE) when handling the compound. [16]
- Toxicological Profile:
The toxicity of HMDS has been the subject of various studies and investigations. According to the available data, HMDS is generally considered to have low acute toxicity, with an oral LD50 (lethal dose for 50% of the test population) in rats of approximately 1,700 mg/kg [17]. However, prolonged or repeated exposure to HMDS may have adverse health effects.
- Inhalation Hazards:
Exposure to HMDS vapors can be harmful if inhaled. Prolonged inhalation may cause respiratory irritation, headaches, dizziness, and drowsiness. [18] In high concentrations, HMDS vapors can displace oxygen, leading to potential asphyxiation. Appropriate ventilation and the use of respiratory protection, such as a suitable respirator, are recommended when working with HMDS.
- Skin and Eye Irritation:
HMDS can be irritating to the skin and eyes upon direct contact. Exposure may cause redness, dryness, and a burning sensation [18].The use of appropriate PPE, such as chemical-resistant gloves and goggles, is essential to prevent skin and eye contact.
- Long-term Health Effects:
While the available data suggests that HMDS has low acute toxicity, there is limited information on the potential long-term health effects associated with chronic exposure. Some studies have indicated that prolonged exposure to HMDS may have adverse effects on the liver and kidneys [19]. Caution is advised, and exposure should be minimized to reduce the risk of any long-term health consequences.
- Environmental Considerations:
HMDS is considered a volatile organic compound (VOC) and can contribute to air pollution if released into the environment [20]. Appropriate disposal methods and containment measures are essential to minimize the environmental impact of HMDS-containing waste.
In conclusion, while HMDS is a valuable and widely used organosilicon compound, it is crucial to exercise caution and adhere to proper safety protocols when handling and working with this substance. Adherence to established safety guidelines, the use of appropriate PPE, and proper ventilation and disposal methods can help mitigate the potential risks associated with HMDS. Ongoing research and monitoring are essential to further understand the long-term health and environmental implications of HMDS exposure.
1. Barton, T.J., & Boudjouk, P. (1990). Organosilicon chemistry: A brief overview., Organosilicon chemistry: A brief overview. (1990).
2. Gosar, Ž.Đ., D.; Pevec, S.; Gergič, B.; Mozetič, M.; Primc, G.; Vesel, A.; Zaplotnik, R. Distribution of the Deposition Rates in an Industrial-Size PECVD Reactor Using HMDSO Precursor. Coatings 2021, 11, 1218. https://doi.org/10.3390/coatings11101218, Distribution of the Deposition Rates in an Industrial-Size PECVD Reactor Using HMDSO Precursor. 2021.
3. Şanli, D.D.o.c.o.s.a.w.h.-t.p.d., Development of composites of silica aerogels with hydroxy-terminated poly (dimethylsiloxane). (2014). .
4. Gilman, H., & Dunn, G. E. (1953). Relationships between Analgous Organic Compounds of Silicon and Carbon. Chemical Reviews, 52(1), 77-115., Relationships between Analgous Organic Compounds of Silicon and Carbon. . (1953).
5. Dzugan, S.J.F.i.m.-c.b.r.w.e.o.a.a.T.F.S.U., Factors influencing metal-carbon bond reactivity with emphasis on aluminum alkyls. (1987).
6. Prakash, G.S., & Yudin, A. K. (1997). Perfluoroalkylation with organosilicon reagents. Chemical reviews, 97(3), 757-786., Perfluoroalkylation with organosilicon reagents. . (1997).
7. Pesek, J.J., & Matyska, M. T. (1997). Methods for the modification and characterization of oxide surfaces. Interface Science, 5, 103-117., Methods for the modification and characterization of oxide surfaces. (1997.
8. Weibel, G., Eggenberger, U., Kulik, D. A., Hummel, W., Schlumberger, S., Klink, W., … & Mäder, U. K. (2018). Extraction of heavy metals from MSWI fly ash using hydrochloric acid and sodium chloride solution. Waste management, 76, 457-471., Extraction of heavy metals from MSWI fly ash using hydrochloric acid and sodium chloride solution. (2018).
9. Royo, F.L.F.o.s.p.d.H.o.S.P., 611-677., Fabrication of silicon photonics devices. (2013.
10. Tian, D., Song, Y., & Jiang, L. (2013). Patterning of controllable surface wettability for printing techniques. Chemical society reviews, 42(12), 5184-5209., Patterning of controllable surface wettability for printing techniques. (2013).
11. MacDonald, S.A., Willson, C. G., & Frechet, J. M. (1994). Chemical amplification in high-resolution imaging systems. Accounts of Chemical Research, 27(6), 151-158., Chemical amplification in high-resolution imaging systems. (1994).
12. Sartori, G., Ballini, R., Bigi, F., Bosica, G., Maggi, R., & Righi, P. (2004). Protection (and deprotection) of functional groups in organic synthesis by heterogeneous catalysis. Chemical Reviews, 104(1), 199-250., Protection (and deprotection) of functional groups in organic synthesis by heterogeneous catalysis. (2004).
13. Wang, H.M.D., Chen, C. C., Huynh, P., & Chang, J. S. (2015). Exploring the potential of using algae in cosmetics. Bioresource technology, 184, 355-362., exploring the potential of using algae in cosmetics. (2015).
14. Ivanova, E.V., Minyaylo, E. O., Temnikov, M. N., Mukhtorov, L. G., & Atroshchenko, Y. M. (2023). Silicones in Cosmetics. Polymer Science, Series B, 65(5), 578-594., Silicones in Cosmetics. Polymer Science, Series B. (2023).
15. Zeng, Q., Zhou, H., Huang, J., & Guo, Z. (2021). Review on the recent development of durable superhydrophobic materials for practical applications. Nanoscale, 13(27), 11734-11764., Review on the recent development of durable superhydrophobic materials for practical applications. (2021).
16. Li, S., Yu, L., Xiong, J., Xiong, Y., Bi, S., & Quan, H. (2022). Facile fabrication of superhydrophobic and flame-retardant coatings on cotton fabrics. Polymers, 14(23), 5314., Facile fabrication of superhydrophobic and flame-retardant coatings on cotton fabrics. (2022).
17. Lassen, C., Hansen, C. L., Mikkelsen, S. H., & Maag, J. (2005). Environmental project No. 1031 2005 Miljøprojekt. Danish Ministry of the Environment., Environmental project No. 1031 2005 Miljøprojekt. (2005).
18. Chen, C.Y., Chang, K. C., Huang, C. H., & Lu, C. C. (2014). Study of chemical supply system of high-tech process using inherently safer design strategies in Taiwan. Journal of Loss Prevention in the Process Industries, 29, 72-84., Study of chemical supply system of high-tech process using inherently safer design strategies in Taiwan. (2014).
19. Cassidy, S.L., Dotti, A., Kolesar, G. B., Dochterman, L. W., Meeks, R. G., & Chevalier, H. J. (2001). Hexamethyldisiloxane: A 13-week subchronic whole-body vapor inhalation toxicity study in Fischer 344 rats. International journal of toxicology, 20(6), 391-399., Hexamethyldisiloxane: A 13-week subchronic whole-body vapor inhalation toxicity study in Fischer 344 rats. (2001).
20. Do, D.H., Walgraeve, C., Amare, A. N., Barai, K. R., Parao, A. E., Demeestere, K., & Van Langenhove, H. (2015). Airborne volatile organic compounds in urban and industrial locations in four developing countries. Atmospheric Environment, 119, 330-338., Airborne volatile organic compounds in urban and industrial locations in four developing countries. (2015).
Reaction Conditions and Mechanism of Di ethyl ether
The choice of reaction conditions, such as temperature, pressure, solvent, and catalyst, can significantly impact the yield and selectivity of diethyl ether synthesis. For example, in the dehydration of ethanol over HZSM-5 zeolite, a higher Si/Al ratio and lower concentration of ammonium sulfate modifier were found to give the best performance[1]. Optimal conditions were determined to be a 1:4 molar ratio of ethylene glycol to ethanol, 7 MPa pressure, and 180°C for 4 h, resulting in 69.17% glycol conversion and 67.81% yield of glycol ethers[1].
Mechanistic studies have shown that the dehydration of ethanol to diethyl ether and ethylene on γ-Al2O3 proceeds through a common surface intermediate, which can be inhibited by the formation of ethanol-water dimers at lower temperatures (<500 K). At higher temperatures (>600 K), ethanol dehydrogenation to acetaldehyde and ethane also becomes significant, proceeding via an indirect hydrogen transfer mechanism.
Diethyl Ether Synthesis Mechanism:
The synthesis of diethyl ether from ethanol typically proceeds through an acid-catalyzed dehydration mechanism. The detailed mechanism is as follows:
1. Protonation of Ethanol:
– The first step involves the protonation of the ethanol molecule by the acidic catalyst (e.g., Brønsted acid like H+ from water or a solid acid catalyst like HZSM-5 zeolite). [2]
– This forms a resonance-stabilized ethanol-proton complex
[CH3CH2OH2]+.
2. Elimination of Water (Dehydration):
– The protonated ethanol complex undergoes intramolecular rearrangement, leading to the elimination of a water molecule.[3]
– This forms a carbocation intermediate, [CH3CH2]+, which is stabilized by resonance.
3. Nucleophilic Attack by Ethanol:
– The carbocation intermediate is susceptible to nucleophilic attack by another ethanol molecule.
– The oxygen atom of the ethanol molecule attacks the carbocation, forming a tetrahedral intermediate.
4. Proton Transfer and Elimination:
– The tetrahedral intermediate undergoes a proton transfer, with the proton moving from the oxygen atom to the hydroxyl group.
– This results in the elimination of a water molecule, forming the diethyl ether product.
The overall reaction can be summarized as follows:
2 CH3CH2OH ⇌ CH3CH2OCH2CH3 + H2O
The reaction conditions, such as temperature, pressure, and the nature of the catalyst, can significantly influence the yield and selectivity of the diethyl ether synthesis. Higher temperatures (>600 K) can also promote the dehydrogenation of ethanol to acetaldehyde and ethane via an indirect hydrogen transfer mechanism.
The choice of catalyst, such as the HZSM-5 zeolite with a higher Si/Al ratio and lower concentration of ammonium sulfate modifier, can enhance the performance and selectivity towards diethyl ether production.
References
1. Gang-se, L., Synthesis of Glycol Monoethyl Ether and Glycol Diethyl Ether Using Ethylene Glycol and Ethanol with Heterogeneous Catalysts. Journal of Chemical Engineering of Chinese Universities, 2016. and Synthesis of Glycol Monoethyl Ether and Glycol Diethyl Ether Using Ethylene Glycol and Ethanol with Heterogeneous Catalysts. 2016.
2. Xin, H., Li, X., Fang, Y., Yi, X., Hu, W., Chu, Y., … & Li, X. (2014). Catalytic dehydration of ethanol over post-treated ZSM-5 zeolites. Journal of catalysis, 312, 204-215., Catalytic dehydration of ethanol over post-treated ZSM-5 zeolites. (2014).
3. Kingston, D.G., Hobrock, B. W., Bursey, M. M., & Bursey, J. T. (1975). Intramolecular hydrogen transfer in mass spectra. III. Rearrangements involving the loss of small neutral molecules. Chemical Reviews, 75(6), 693-730., Intramolecular hydrogen transfer in mass spectra. III. Rearrangements involving the loss of small neutral molecules. (1975).
Mechanism of Sodium Methoxide
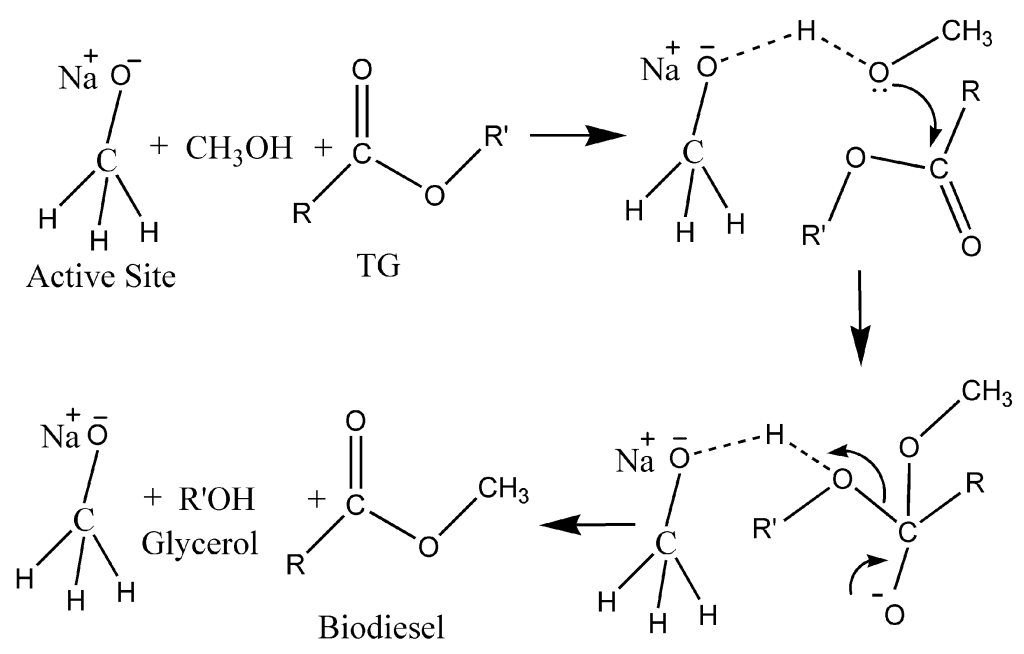
Figure 1Plausible homogeneous catalytic mechanism of transesterification of WCO using NaOMe/zeolite[1]
- Brønsted Base Properties:
The high basicity of sodium methoxide is primarily due to the ability of the methoxide anion (CH3O-) to readily accept a proton, forming methanol (CH3OH) and the hydroxide ion (OH-).[12] This proton transfer reaction can be represented as follows:
CH3O- + H+ → CH3OH
The methoxide anion is a strong base, with a pKa value around 15-16, making it a potent proton acceptor1. This Brønsted base reactivity is the foundation for many of the synthetic applications of sodium methoxide, as it can be used to deprotonate acidic protons on a wide range of organic substrates.[[2]]
When sodium methoxide is dissolved in protic solvents like water or alcohols, the methoxide anion can undergo this proton transfer equilibrium, generating the corresponding alcohol (e.g., methanol) and a hydroxide ion. This equilibrium can be influenced by factors such as pH and the presence of other species in the solution.
- Nucleophilic Reactivity:
In addition to its Brønsted base properties, sodium methoxide can also act as a nucleophile, with the methoxide group (CH3O-) attacking electrophilic carbon centers 12.[3] This nucleophilic reactivity is particularly useful in various organic reactions, such as alkylation and esterification.
In alkylation reactions, the methoxide anion can displace a leaving group (e.g., a halide) from an alkyl halide, forming a new carbon-oxygen bond and producing an ether. This substitution reaction can be represented as follows:
R-X + CH3O- → R-O-CH3 + X-
where R represents an alkyl group and X is the leaving group (e.g., a halide).
In esterification reactions, the methoxide anion can act as a nucleophile, attacking the carbonyl carbon of an acyl halide or an anhydride, displacing the leaving group and forming a new ester bond. This process can be depicted as:
R-C(O)-X + CH3O- → R-C(O)-O-CH3 + X-
where R represents an alkyl or aryl group, and X is the leaving group (e.g., a halide or alkoxide).
The dual reactivity of sodium methoxide, both as a Brønsted base and as a nucleophile, makes it a versatile and valuable reagent in organic synthesis. The ability to deprotonate acidic protons and to undergo substitution or addition reactions with electrophilic centers allows for a wide range of synthetic transformations, including alkylations, esterifications, and other important organic reactions.[4], [5]
Reference:
1. Argaw Shiferaw K, M.J., Yu E, Choi E-Y, Tarte NH. Sodium Methoxide/Zeolite-Supported Catalyst for Transesterification of Soybean Waste Cooking Oil for Biodiesel Production. Inorganics. 2023; 11(4):163. https://doi.org/10.3390/inorganics11040163, Sodium Methoxide/Zeolite-Supported Catalyst for Transesterification of Soybean Waste Cooking Oil for Biodiesel Production. 2023.
2. LINDSAY, A.M.-G.S.o.B.A.a.B.O.D.d., Durham University). Mechanism-Guided Studies of Brønsted Acid and Base Organocatalysis. (2010).
3. Terrier, F.M.n.a.s.J.W.S., Modern nucleophilic aromatic substitution. (2013).
4. Clayden, J., Greeves, N., & Warren, S. (2012). Organic chemistry. Oxford University Press, USA., Organic chemistry. (2012).
5. Johnson, S., Meyers, M., Hyme, S., & Leontyev, A. (2019). Green chemistry coverage in organic chemistry textbooks. Journal of Chemical Education, 97(2), 383-389., Green chemistry coverage in organic chemistry textbooks. (2019).
What is Lithium Tert-butoxide?
Lithium tert-butoxide is a chemical compound with the formula LiOC(CH3)3. It is an organolithium compound consisting of a lithium atom bonded to a tert-butoxy (t-butoxy) group, which is a functional group derived from tert-butanol. The tert-butoxide group consists of a central carbon atom bonded to three methyl (CH3) groups and an oxygen atom.
Lithium tert-butoxide is a strong base and a powerful nucleophile, meaning it readily donates electrons and reacts with electrophiles. It is commonly used in organic synthesis, particularly in reactions involving deprotonation and condensation reactions. It can be used as a base to remove a proton from an acidic hydrogen atom, allowing for the formation of carbon-carbon or carbon-heteroatom bonds.
The compound is typically a white or off-white solid and is highly reactive. It should be handled with caution due to its reactivity and sensitivity to moisture and air. Lithium tert-butoxide is usually prepared by reacting lithium metal with tert-butanol in an anhydrous solvent, such as tetrahydrofuran (THF).
Diethyl Malonate Applications
Diethyl malonate (also known as DEM) is a versatile compound that finds numerous applications in organic synthesis. It is an ester derivative of malonic acid and contains two ester groups. The presence of these ester groups makes diethyl malonate a valuable building block in various chemical reactions. Here are some common applications of diethyl malonate in organic synthesis:
1. Malonic Ester Synthesis: Diethyl malonate is widely used in the malonic ester synthesis, which is a powerful method to introduce a carboxylic acid group into organic molecules. In this reaction, diethyl malonate undergoes nucleophilic substitution with alkyl halides or other electrophiles to form substituted malonic esters. The resulting malonic esters can be further modified through decarboxylation, hydrolysis, or other chemical transformations.
2. Knoevenagel Condensation: Diethyl malonate participates in the Knoevenagel condensation reaction, which is a useful carbon-carbon bond-forming reaction. It reacts with aldehydes or ketones in the presence of a base to give α,β-unsaturated carboxylic acids or their derivatives. This reaction is widely employed in the synthesis of a variety of compounds, including pharmaceuticals, dyes, and natural products.
3. Synthesis of Barbiturates: Diethyl malonate serves as a key starting material in the synthesis of barbiturates, which are a class of drugs with sedative, hypnotic, and anticonvulsant properties. By reacting diethyl malonate with urea and an appropriate aldehyde or ketone, barbiturate derivatives can be obtained.
4. Synthesis of α-Amino Acids: Diethyl malonate can be used for the synthesis of α-amino acids through a multi-step reaction sequence known as the malonic ester synthesis. By selectively alkylating one ester group, followed by hydrolysis, decarboxylation, and further modifications, α-amino acids with various side chains can be obtained.
5. Synthesis of Heterocycles: Diethyl malonate participates in the synthesis of various heterocyclic compounds. For example, it can undergo cyclization reactions, such as the Dieckmann condensation, to form five- or six-membered rings. These reactions are useful for the synthesis of natural products, pharmaceuticals, and other biologically active compounds.
Titanium IV Ethoxide Applications
Titanium IV ethoxide, also known as titanium tetraethoxide or titanium(IV) tetraethoxide, is a chemical compound with the formula Ti(OC2H5)4. It is a versatile compound with several applications in various fields. Here are some common applications of Titanium IV ethoxide:
1. Sol-gel Processing: Titanium IV ethoxide is widely used in sol-gel processing, which is a technique for the fabrication of ceramic and glass materials. It serves as a precursor for the deposition of thin films, coatings, and nanoparticles. It can be hydrolyzed and condensed to form titanium dioxide (TiO2) structures with controlled properties, such as porosity, morphology, and crystallinity.
2. Photocatalysis: Titanium dioxide is a well-known photocatalyst, and Titanium IV ethoxide is a precursor for the production of titanium dioxide nanoparticles. These nanoparticles exhibit excellent photocatalytic properties, which can be utilized for the degradation of organic pollutants, water purification, and self-cleaning surfaces in applications like paints, coatings, and solar cells.
3. Nanotechnology: Titanium IV ethoxide is employed in the synthesis of titanium-based nanoparticles, including titanium oxide, titanium carbide, and titanium nitride nanoparticles. These nanoparticles find applications in various fields such as electronics, energy storage, catalysis, and biomedical devices.
4. Surface Modification: Titanium IV ethoxide can be used as a surface modifier for various substrates, including metals, ceramics, and polymers. It can form a thin, adherent, and protective titanium oxide layer on the surface, enhancing the substrate’s corrosion resistance, mechanical properties, and biocompatibility.
5. Chemical Vapor Deposition (CVD): Titanium IV ethoxide can be utilized as a precursor in chemical vapor deposition processes to deposit thin films of titanium dioxide. CVD is widely employed in the semiconductor industry for the production of integrated circuits, optical coatings, and other thin-film applications.
6. Antimicrobial Coatings: Titanium dioxide nanoparticles derived from Titanium IV ethoxide can be incorporated into coatings to provide antimicrobial properties. These coatings are used in various applications such as healthcare facilities, food packaging, and consumer products to inhibit the growth of bacteria, fungi, and viruses.
7. Dye Sensitized Solar Cells (DSSCs): Titanium IV ethoxide is a crucial component in the fabrication of dye-sensitized solar cells. It acts as a precursor for the mesoporous titanium dioxide layer that serves as the photoanode, facilitating the absorption of light and electron transport in these types of solar cells.